CREATING A SAFETY CULTURE. 2,566 DAYS ACCIDENT FREE
Safety - Achieving the Goal of Zero Accidents
Midwestern Contractor's 12-year story of the commitment and determination required to create a culture of safety. How they developed management strategies, utilized mobile devices and cloud computing, to enable a fresh approach to safety; and the results of those efforts; a 1-year, 2.3-year and 3.7-year, back-to-back spans of time totaling 2,566 days with zero incidents or accidents. The injuries that did interrupt these periods were minor, requiring only first aid.
This is a case study about Midwestern Contractor’s (MWC), quest to create a culture of safety where no one gets hurt.
Midwestern Contractors was founded in 1951. Safety has always been a part of project planning and execution. The Distribution Contractors Association (DCA) safety award is named after one of MWC’s founders Arthur T. Everham. Mr. Everham knew that bad things can happen very quickly during pipeline and station construction. He helped develop the company’s first safety program and built safety planning into every project. MWC won that award twice, he believed in safety and, so does MWC.
Within the last decade new focus was placed on safety by contractors and the operating companies. The direction was clearly towards the elimination of all accidents and incidents.
At MWC, around 2010 to 2015, the Company gathered plenty of safety documentation. It was all on paper and included excavation checklists, equipment inspections and jobsite audits to name a few. This paperwork originated on the jobsite, was given to the superintendents and ultimately reached the safety department where it was sorted and entered in spread sheets for analysis. It could take days before a field safety audit was entered. With crews spread across a multi-state region it was difficult to gather, assess and act upon leading indicators. The result was reaction to incidents and accidents. These actions included root cause analysis, safety stand downs and more checklists. This cycle repeated. Forward progress towards improvement was hard to achieve. The TRIR and EMR bounced around. The EMR remained under 1.
During this time customer demands for safety, environmental and quality assurance continued to increase. Contractors had to adapt and improve or be left behind. Each project required more front-end preparation, including safety, environmental and quality plans for every aspect of the work, e.g., confined space, atmospheric monitoring, lift plans, lock-out-tag-out, erosion control, welding, coating, and excavation. Our Safety and Project Management staff was stretched thin and sight safety oversight was impacted.
It is important to note that the requirements for planning and executing a project safely also required the collection, processing, and storage of more information. Fortunately cloud computing became the vehicle that allowed the Company to move and process information faster. Management realized that they were in a reactive safety management environment and it needed to be changed.
CREATING A NEW CULTURE OF SAFETY
More safety officers were hired. More importantly management took on safety as a primary mission. They went into the field and performed audits. This ongoing effort was done by the president, vice-president, and PM’s. The importance of safety was emphasized as a primary mission and in a non-threatening way. The idea was to build a culture of continuous improvement by sharing information and encouraging participation. Management was intent on building this new culture. It was a very high priority and there was no room for those who did not believe in the mission.
The MWC IT department authored Construction View™. For the first time the Company had a system that could organize all job related information in a relational database. All foremen were equipped with an iPad and iPhone. Now documents, photos, and videos could be sent from field to office and back in near real time. We developed our own URL “GoodSafetyCatch.com” and created a reporting system for near misses. The real time nature of this system flagged the safety officers when a “Good Catch” or near miss occurred. This in turn, enabled the safety officers to respond and implement mitigation strategies company wide. If there was an issue with rigging, pinch points, or line of fire proximity on one crew, it very likely was occurring on another. Cloud computing helped management better utilize leading indicators. Management also helped the safety department by engaging field personnel in meaningful safety conversations and reinforcing company HSE policies. It was important for field personnel to see and hear how committed the company was to their safety.
In addition to the job site safety audit requirements, superintendents and project managers continued to engage field employees in discussing hazards on the job site.
Maintaining a leadership emphasis on safety, management also gave the field crews feedback on their project successes. Negative events are addressed with the aim to improve and prevent it from happening again. Positive feedback is also given when tasks or projects are completed incident free. Often this is celebrated with a token recognizing this level of performance, the crew is also featured on the company website or LinkedIn page.
TRAINING & COMMUNICATION
In the past training programs were delivered annually; at the time of onboarding for new hires; or in the form of toolbox talks. All training was conducted in person in a group setting. MWC made the following changes. Frequency of topic specific training was increased to quarterly regardless of the customer demands for schedules and deadlines. All personnel received OSHA -10 hour while Superintendents and foremen received OSHA 30-hour training. Quality and consistency of training was improved, and attendance was mandatory.
A weekly safety teleconference was started with foremen, superintendents, and management to address the most current hazards and/or good catches observed on each of the projects during that week of work. This led to heightened awareness of each project's hazards and how to deal with them. This information was given to the crews during their toolbox talks. This line of communication created synergy among the foremen, superintendents, PM’s and management and kept everyone thinking ahead about potentially hazardous tasks and how to deal with them.
ENCOURAGING PEER INVOLVEMENT
MWC management knew that their employees could not be passive recipients of safety training and talks. They had to be involved. To that end we asked the superintendent and foreman to designate a crew member to be the safety representative on each project. This employee set an example for the entire crew by verifying currency of fire extinguisher tags, gas monitors, fall protection harnesses, rigging and lifting equipment certification, and other safety related tasks. They also participated in weekly audits. Any non-compliant items were immediately dealt with. We saw an improvement in attention to detail and less complacency.
One simple way of engaging employees is to ask what their job responsibilities are at that moment. They should be able to describe the company’s and customer’s expectations, their tasks, the hazards associated with them and mitigations that they can take to reduce and prevent those hazards. All field management and office management site audits now include discussions with crew members on the above questions. If an employee is unable to answer a specific question, then that employee will be required to complete additional training to address the deficiencies.
Quarterly safety training meetings provided another opportunity to seek employee feedback on the company's current safety challenges. Field employees participate in crafting changes or additions to company safety policies. Field employees give short presentations or lead discussions on certain topics. This helps the safety department to work on new and more effective ways to present information at training.
To encourage greater participation by all crew members, the foreman designates a crew member to lead the tailgate safety meeting before the start of a shift. The designated employee will review the specific tasks planned, hazards associated with each task, as well as mitigation measures. The foreman can fill in additional hazards and mitigations with the crew before activating the Hazardous Work Authorization (HWA).
After required HWA documentation has been completed the entire crew performs a site walk. The purpose of the site walk is to identify any additional hazards previously missed in the morning hazard assessment meeting. All additional hazards identified will be documented on the daily HWA along with appropriate mitigation measures.
These changes have created engagement and heightened safety awareness among the management team, superintendents, foremen and crew.
A NEW ROLE FOR CLOUD COMPUTING
In 2017 the company set up a commercially developed Safety Management System (SMS). Our combination of GoodSafetyCatch.com and our existing ConstructionView™ was not optimized for safety analytics. The SMS was set to deliver the type of analysis that would allow the safety department to visualize the big picture across all crews spread over an entire region. After a few months of set up the data began to flow via cloud computing from field to the SMS. The safety department was able to streamline communications even further by following up on near misses and broadcasting mitigations to all concerned parties. This stopped many phone calls from different levels of management and the foreman having to repeat the story numerous times. The system was also fast. A near miss notification and mitigation could be turned around in under 24 hours. Safety audits with significant findings, affecting all crews, are now disseminated in 24 hours or less. This was revolutionary for the Company and it has resulted in a 1 year, 2.3 year and 3.7 year, back-to-back spans of time with zero incidents or accidents. Furthermore, the incidents that did occur were minor requiring only first aid.
The SMS brought the safety picture into focus and allowed the safety team and management to act on and emphasize leading indicators before they evolved into incidents or worse, accidents.
The above charts are representative of the way data can be displayed in the SMS. Many other reports are available. The SMS is an accounting system for safety officers. By using this data, they can spot trends and act on them. Without the accumulation of data from near misses, incidents and safety audits, safety personnel are blind to the big picture and can only react when something happens.
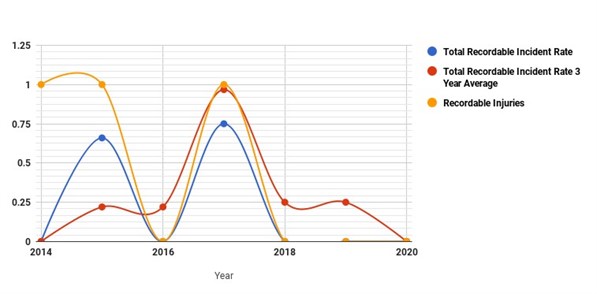
Total Recordable Incident Rate (TRIR)
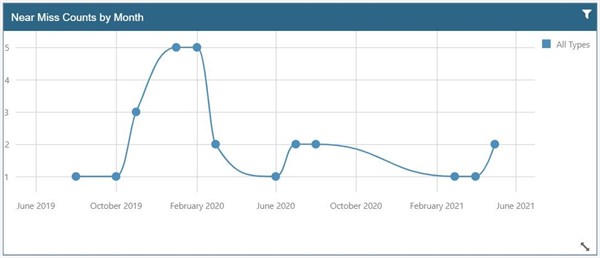
Near misses by month 2019 to 2021
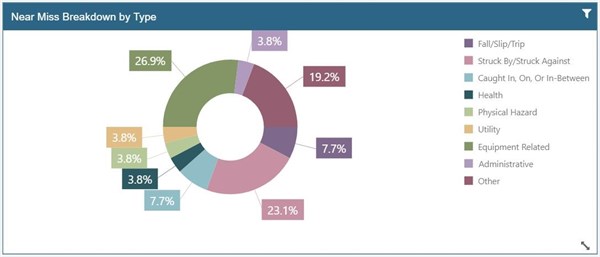
Near misses by type
THE FUTURE
As the SMS accumulates data more trends will emerge, and new strategies will be developed by management and safety to head off the potential consequences that the trends indicate. More attention to leading indicators and the engagement of all hands will help to contain the leading indicators and prevent them from changing into an incident or accident.
Training will be moved to a combination of online instruction with more employees acquiring certified skills in traffic control, work zone protection, rigging, etc. Practical instruction will supplement the online work. The benefit will be better recording and management of all training courses, their expiration dates and tracking each employee’s certificates. Most of this training will be delivered during downtimes in the winter or in between projects. We will build a stronger more educated workforce.
SUMMARY
Safety is a scaffold constructed of responsible human behavior, attention to detail, discipline, and sound procedures. The structure for achieving an accident and incident free workplace must be maintained and looked after constantly. It is expensive, but the payoff is real. For over 3 and a half years MWC employees have been injury free. No trips to the hospital, no lost time, no therapy. While the Company has not reached zero accidents, they have, over almost seven years, seen their accidents diminish to three minor ones during that period. The employees are 100% onboard, and have acquired a heightened degree of safety awareness. We hope this becomes an ingrained habit that spills over into their personal lives. Stop – Think – Act – Review, a good way to conduct life.
COMPANY PROFILE
Midwestern Contractors (MWC) founded in 1951 provides skilled tradesmen, project and safety management to the oil and gas industry. Based in Northern Illinois and operating in the northern tier of the Midwest from Nebraska to Pennsylvania, their projects include stations, laterals, M & R, integrity, relocations, exposures, lowering and piping modifications. Midwestern Contractors believes in:
- Culture of Success - A relentless desire to communicate, execute, succeed, and deliver quality services at every level
- Professionalism - A reputation built through performance, honesty, integrity, and a team mindset.
- Responsiveness - Dependability. A willingness and ability to meet changing customer demands.
- Employee Purpose - To grow professionally by learning new skills, embracing new challenges and by striving to have a positive impact on the people in our lives.
Contact Midwestern Contractors: info@midwesterncontractors.com