Monday, April 18, 2016
HDD Pipe Extraction (Video Content)
When it comes to repairing a pipe drilled in by horizontal drilling methods operators are sometimes left with few options. On a recent Ohio project a right-of-way corridor was very congested with existing pipe that had been drilled in. This 12" pipe, all 0.500' wall, had been in the ground for many years. One pipe in particular was showing signs of internal and external problems. These problems were significant enough to cause the operator to make the decision to replace the pipe. No room existed for a new drill. The only option was an extraction.
Extracting 2,400' of 12" pipe requires detailed planning and flawless execution. Still there is risk in the operation.
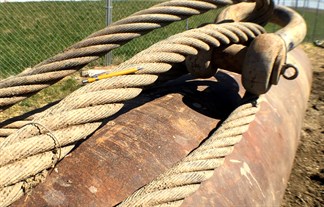
Rigging, note pencil
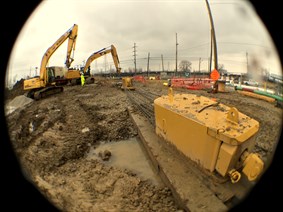
Five part blocks rigged
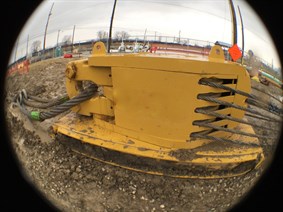
Block close up weight (10,000lbs)
Setting 68 tons of steel pipe in motion is very much a matter of accurate and proper attachment of the rigging and percussion equipment, and the gentle application of force. There is a choreography to the extraction process. The successful application of 200,000 pounds of force to a 2,400' pipe previously bored into the earth depends on skilled hands that are very easy on the throttles. Finesse wins every time over brute strength. The Grundorams supplied by TT Technologies (See http://www.tttechnologies.com/) are sized for the project. The hammer speed can be varied from 50 to 180 strokes per minute. The attachment requirements are very precise, the angle of extraction is equally precise. The accuracy of alignment will preserve the weld joints much longer into the process.
Tension alone will not come close to moving a 68 ton mass of steel pipe or overcome the friction forces of the pipe's wall against the earth. But the combination of tension and the judicious application of percussive force can add sufficient power and vibration to overcome the inertia of the pipe's mass. Tension force prevents the mass from reverting to its original position and allows any movement to be maintained when applying percussive force. This combination of a point force combined with a steady pull actually imparts movement to the pipe mass and once in motion it becomes easier to maintain the movement. It is thought that some liquifaction of the old drilling mud may take place at the pipe wall to soil interface. This also aids the process of extraction by imparting energy into the old drilling mud causing it to act as a lubricant.
In this project two air hammers, two five part steel blocks on sleds, and two D8 CATS, applying a combined force of over 186,000 pounds of force were utilized to make the pipe move. After movement began the force rapidly diminished to 52,000 lbs as the pipe was withdrawn. The air hammers were only used at 25-30% throttle. It was enough to do the job.
Of course the other advantage of pipe extraction is the fact that the new pipe can be welded up in advance, hydro-tested and pulled in by welding it to the old pipe. This is exactly what we did to give our customer a new hydrotested pipe ready to be placed into service.
Missteps could have occurred during this project. The extraction pipe could have failed in place, the pipe could have been distorted and become wedged in place, the welds could have separated. The only guarantee of success is proper planning and careful execution.
Our team consisted of Midwestern Contractors, Laney Directional Drilling (http://www.laneydrilling.com/) and TT Technologies (http://www.tttechnologies.com).
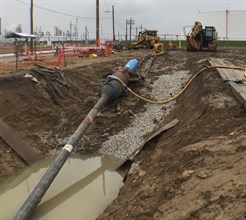
Grundoram connected
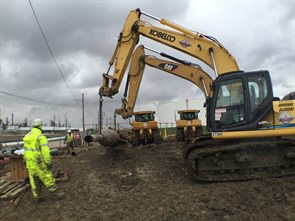
Track Hoes repositioning Grundoram
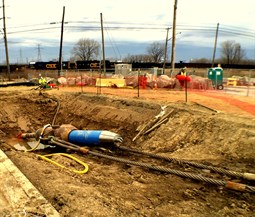
Grundoram ready for next pull

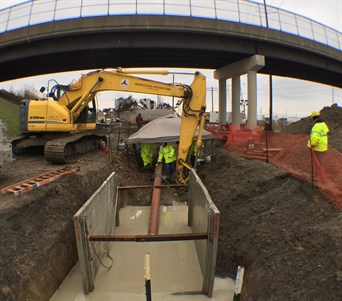
VIDEO CONTENT
Project Notes:
- Extraction pipe consisted of 2,400' of 12" 0.500" wall
- Replacement pipe consisted of 2,400' of 12" 0.500" wall
- Total welds = 60 requiring 7 passes for each weld
- Additional welds required to join 0.717" wall to 0.500" for Grundoram air hammers
- Pipe string weight approximately 68 tons
- Two Grundoram Air Hammers and casings
- Two five part steel blocks mounted on sleds
- Two D8 Cats
- Two Cat 336E excavators
- Extraction rate 400'/day (Limited work space, pipe had to be cut and the pull reset)
Project Safety Notes:
- Spring weather conditions
- High winds, cold temperatures, thunderstorms lightening
- Site conditions were dangerous with mud and standing water a constant challenge
- High energy potentials generated when tension was applied to the rigging
- Heavy machinery moving in tight quarters
- Industrial location with heavy truck and rail traffic
- Overpasses caused overhead obstructions
- Many in-ground utilities requiring hydro-excavation
No incidents or accidents occurred on this project. The entire team functioned as a unit with the work and safety planning and project execution.
Three views of drill string
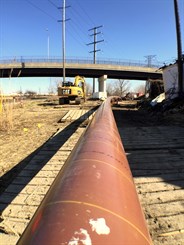


Midwestern Contractors works throughout the Midwestern States. Our geographical footprint includes Ohio, Pennsylvania, Indiana, Kentucky, Tennessee, Illinois, Missouri, Kansas, Nebraska, Iowa, Minnesota, Wisconsin, Michigan. This case study illustrates the planning, and team work required to successfully work on critical assets. We value the confidence our customers place in us to carry out projects like this one. A sincere thank you to our superintendents, foremen, crews, Laney crews and TTTechnologies' consultants for a job well done.
Thanks to Ztylus for the 4:1 iPhonography equipment used in this article see www.Ztylus.com