Thursday, March 24, 2016
1400' Horizontal Directional Drill Project (Video Content)
The scope was simple, auger under a road and push pipe through, drill 1,400' and pull back pipe, and finally open cut and tie it all together. But Not everyone can wake up, go to work and drill a big hole in the ground that goes in at one point and comes up precisely at another, some 1,400' away. In our pipeline and utility world it happens all the time. It is the best way to get pipelines under rivers, roads and rail roads. Midwestern Contractors has gotten good at it. Acting as the General Contractor we recently undertook a project to relocate a pipeline under and around a road construction project by using Horizontal Directional Drilling (HDD) and an Auger bore. The entire relocation was 1,700'. the working space was cramped, traffic had to be flowing on the adjacent arterial road. The drill string was laid out in a curved area with no straight line entry into the drill hole. These were just a few of the challenges our Project Manager and Superintendent faced on this job.
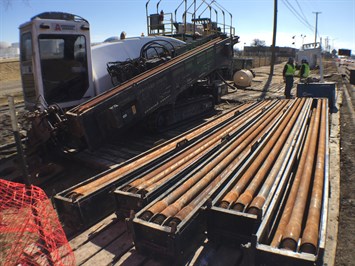
Drill machine and stem set up
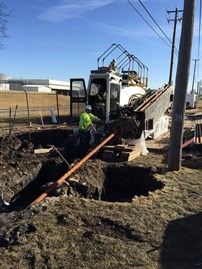
Drilling pilot hole
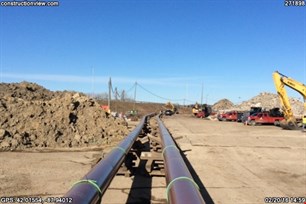
Welding Pipe String
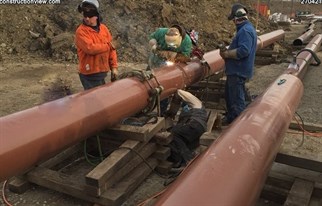
Welding Pipe String
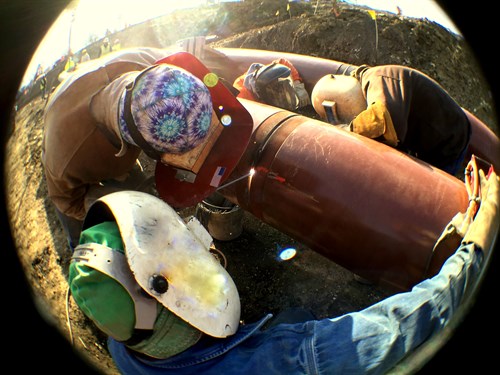
M. Purpura Photos
Planning for this project started in the fall of 2014 with bid documents released in 2015 and work starting in the winter of 2016. This congested interchange is being transformed into a diverging diamond configuration. Numerous pipelines, sewer, water, power and telecommunications lines are running along this corridor. There are also major water mains crossing the drill path, and a combination of residential and commercial ingress and egress across the drill path.\
The laydown area was occupied with work on a 90" water main and was cleared out just in time to recieve the 50 sticks of pipe and fittings required for the project. Our crews helped clear out the laydown yard and offload the pipe. Then the drill path, drill entry and drill exit points were prepped prior to bringing in the drill rig. Traffic control measures and signage were put into place. Mats were laid, and all utilities were pot holed, identified and labeled with the depth to the utility. At the same time our drill string crews mobilized in we began stringing and cribbing pipe. Welding also started up and the 700' string sections began to take shape.
After the drill rig was brought the drillers began boring the pilot hole. In addition to Utility Damage Prevention Planning, Midwestern Contractors also follows an Inadvertent Release Plan in the event of frac outs during the drilling process. These two planning documents enable us to avoid utility damage and to respond quickly and professionally to any type of inadvertent release wherever and whenever they may occur.
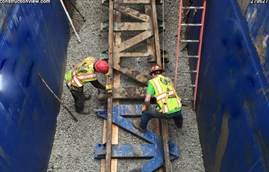
Photo Credit: Steve Olsen
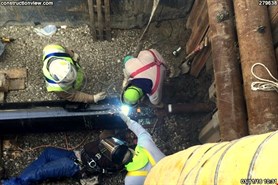
Photo Credit: Steve Olsen
VIDEO CONTENT
The pilot hole proceeded smoothly through gravelly clay material at a depth of over 40 feet. Welding production was ahead of schedule when the pilot bit emerged precisely on location. The reaming operation proved to be challenging due to areas of heavy clay clogging the reamer and slowing progress. During this slow down we shifted the welders over to the auger bore which picked up the pipe at a point of intersection and carried it under the arterial roadway. This string was welded, and coated in preparation for the bore.
With reaming on the 1,400' drill complete the pullback was scheduled and executed without interruption. The reaming operation was somewhat tedious due to heavy clay and frequent clogging of the reamer. The two 700' strings were joined and the pull back continued. Construction traffic entering and leaving the site had to exercise extreme caution due to the volume of traffic and frequent lane closures and realignments carried out by the highway construction that was ongoing during our project.
Project Facts:
- Drill length: 1,400'
- Drill depth: 60'
- Number of days for pilot hole: 7
- Number of days for reaming: 15
- Inches of weld: 2,000
- Pipe diameter 16"
- Maximum shoring depth: 29'
- Auger bore 180'
- Cubic yards of earth moved: 150
- Number of crane mats required: 100
- Soil type: compacted hard clay and gravelly clay
A small 200' section of open cut was made more difficult by the exit angle of the drill. This excavation required excavation to install engineered shoring. This allowed crews to safely work 29' below grade. Ground water infiltration was a problem. Pumps were running continuously as the drill pipe was cut back. Fittings were welded in place to reduce the angle of the pipe and to make the tie-in simpler. The entire 1,800 foot assembly was then hydrotested for continuity.

Reverse color view of welder's hand tools
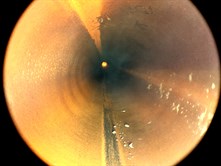
View of arc welding from end of 40' pipe
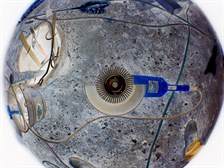
M. Purpura photos
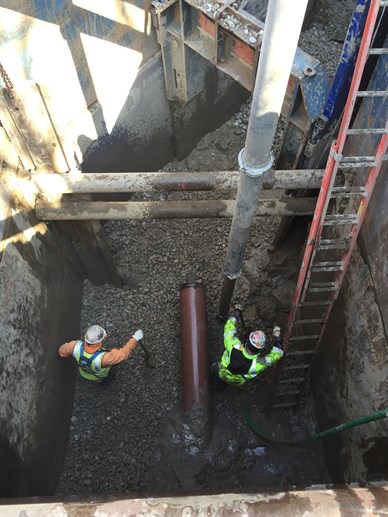
29' Deep engineered shoring in place for open cut tie-in section, (Steve Olsen Photo)
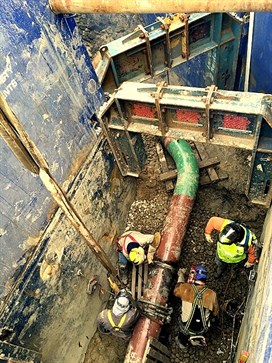
Welding offset from drill pipe to auger bore (J. Pfleeger Photos)
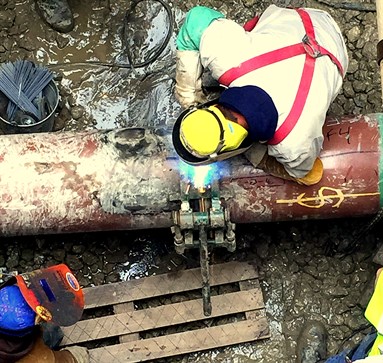
Welding offset from drill pipe to auger bore (J. Pfleeger Photos)
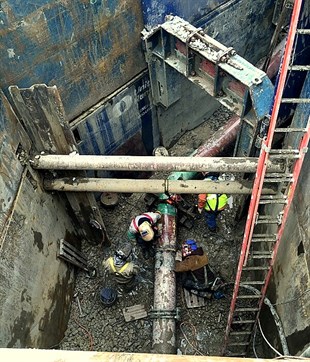
Welding offset from drill pipe to auger bore (J. Pfleeger Photos)
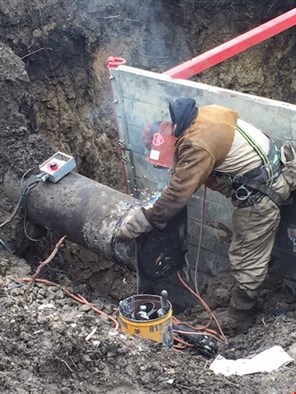
Plating pipe
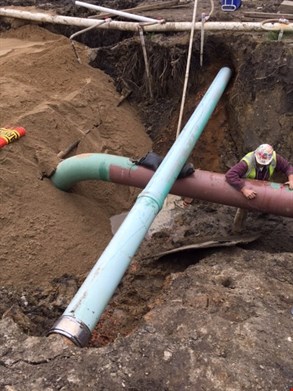
Crossing a gas line
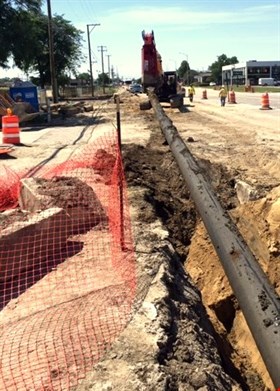
Removing old pipe
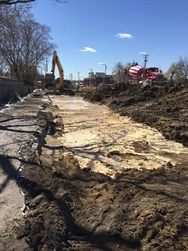
Flowable Fill in open cut section
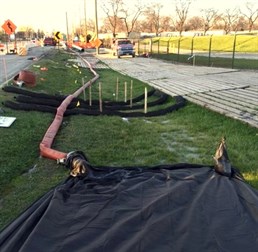
Water filtration
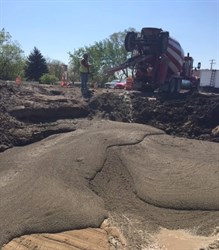
Flowable fill in tie in area
After the drill a gauge plate was pushed through the pipe, no deformation occurred. When the offset was welded more pipe was lowered into the excavation in preparation for tie-in.
Projects like this one are complex. They require diligence on the part of all parties to carry out safely and to achieve high quality results. The work, once completed must last for decades and every detail of the job is important. We thank our crews, subcontractors, foremen, and our customer for working as a team to make projects like this one a success. Midwestern Contractors delivers pipeline construction and maintenance services throughout the Midwest including Michigan, Ohio, Indiana, Illinois, Pennsylvania, Wisconsin, Minnesota, Iowa, Nebraska, Kansas and Missouri.
After completing the tie-in the project continued with the removal of the deep shoring systems, sand padding around the pipe, then backfill with flowable fill material and restoration work. All the while traffic control was still in place and surface water was managed and routed to filter bags before discharge back to ground water. One other aspect of the project was the removal of the old pipe which was originally placed at a depth of cover of 50 inches. The sections that could not be removed were plated, grouted and abandoned in place. The following photos tell the story and show some of the steps required to complete a project like this one.
Final pipe removal and restoration took place in August of 2016. Much of the old pipe was sheared into transportable lengths as it was removed. There is a lot of work on the front and back ends of the actual drilling process. This particular project was complicated by the cramped working corridor, traffic, and surrounding construction activities associated with the highway expansion work.
Thanks to Ztylus.com for the 4 in 1 iPhonography lens kit, and to Steve Olsen and Jon Pfleeger for their photos submitted through Construction View. For information on Construction View contact info@midwesterncontractors.com