Friday, September 27, 2019
LNG Maintenance Project
Natural gas is abundant in the United States thanks to innovative drilling techniques and the use of hydraulic fracturing. Once released, this gas, must be transported for use, stored or flared off. Natural gas is made up mostly of methane, four hydrogen atoms attached to one carbon atom. This simple molecule burns clean which is why natural gas is useful for home heating and industrial process heat.
A drawback of natural gas is the difficulty storing large quantities of gas. For years certain geologic formations have been utilized to store it. Usually by means of high-pressure injection into deep formations of sandstone capped by denser limestone. When this method is used contaminants are introduced into the gas from Brine and any other minerals mixed into it. These contaminants then must be removed from the gas before it can be pressurized and sent to market. Liquification is another means of storing natural gas.
Gas, like water, has phases. The liquid phase of natural gas occurs at -260 °F. In the liquid phase 1 Ft³ of Liquified Natural Gas (LNG) = 600 Ft³ of natural gas in the gaseous state. LNG facilities with their insulated tanks, are an ideal way to store gas. LNG is also good for transporting gas by specialized transport ships. The liquified gas can then be returned to the gaseous state for use when demand for heat is high or for export purposes.
Midwestern Contractors has worked on high- and low-pressure gas supply systems for years. On one recent project we were called upon to replace piping and install piping modification to an LNG storage and processing plant.
The process of cooling and storing natural gas involves the removal of heat until the gas becomes liquid, then it is stored in insulated tanks to prevent vaporization, and finally re-heating the gas to drive it into a vaporized state where it will then be compressed and sent into a pipeline to a larger market. The steel pipes that are used to safely move gas through a facilities’ refrigeration, storage and vaporization processes experience large temperature variations and subsequently large expansion and contraction cycles. Steel has great ductility but at some point, repeated expansion and contraction will cause it to fail. Our task was to remove insulation, fabricate new pipe assemblies, prime, paint and install those assemblies back into the plant. The inlet and outlet piping were also replaced. This required the installation of a stopple fitting.
Project Notes:
- Pipe diameters 1” to 20”
- Inches of weld 14,530”
- 8,400 Cubic yards of hydro-excavation
- Hot tapped 2-12” stopple fittings
- Installation of 300’ of bypass line
Safety is always top of mind in any project involving flammable materials. In addition, all the fabrications were removed and replaced by using a crane to lift and lower each assembly. Proper rigging, spotting and communication during each “pick” kept the crew and the adjacent facility piping safe. For the underground portion of the work hydro-excavation was used to expose the piping, shoring boxes were employed for the cut out and tie-in phases. Some of the piping was accessed from man walks and scaffolding. The welders and fitters wore harnesses and fall protection equipment. PPE’s were, of course, mandatory.
During the entire project not one safety incident occurred. We owe this safety performance to the diligence and awareness of our entire crew. Superintendent, PM’s, foremen, operators, welders, laborers, all were aware that good safety practices and communication keep people safe and keep the job on schedule.
Challenges on this project centered on the complexity of the fabrications and the tight working quarters. Critical to the success of this project was the ability of our foreman and welders to properly sequence the removal and replacement of each fabrication to avoid blocking the next pipe assembly from removal. Accurate fitting and flawless welding made it much easier to stay on schedule.
Safety – Planning – Management and skilled tradesman make Midwestern Contractors a logical choice for mechanical projects on oil and gas facilities.
CASE STUDY GALLERY
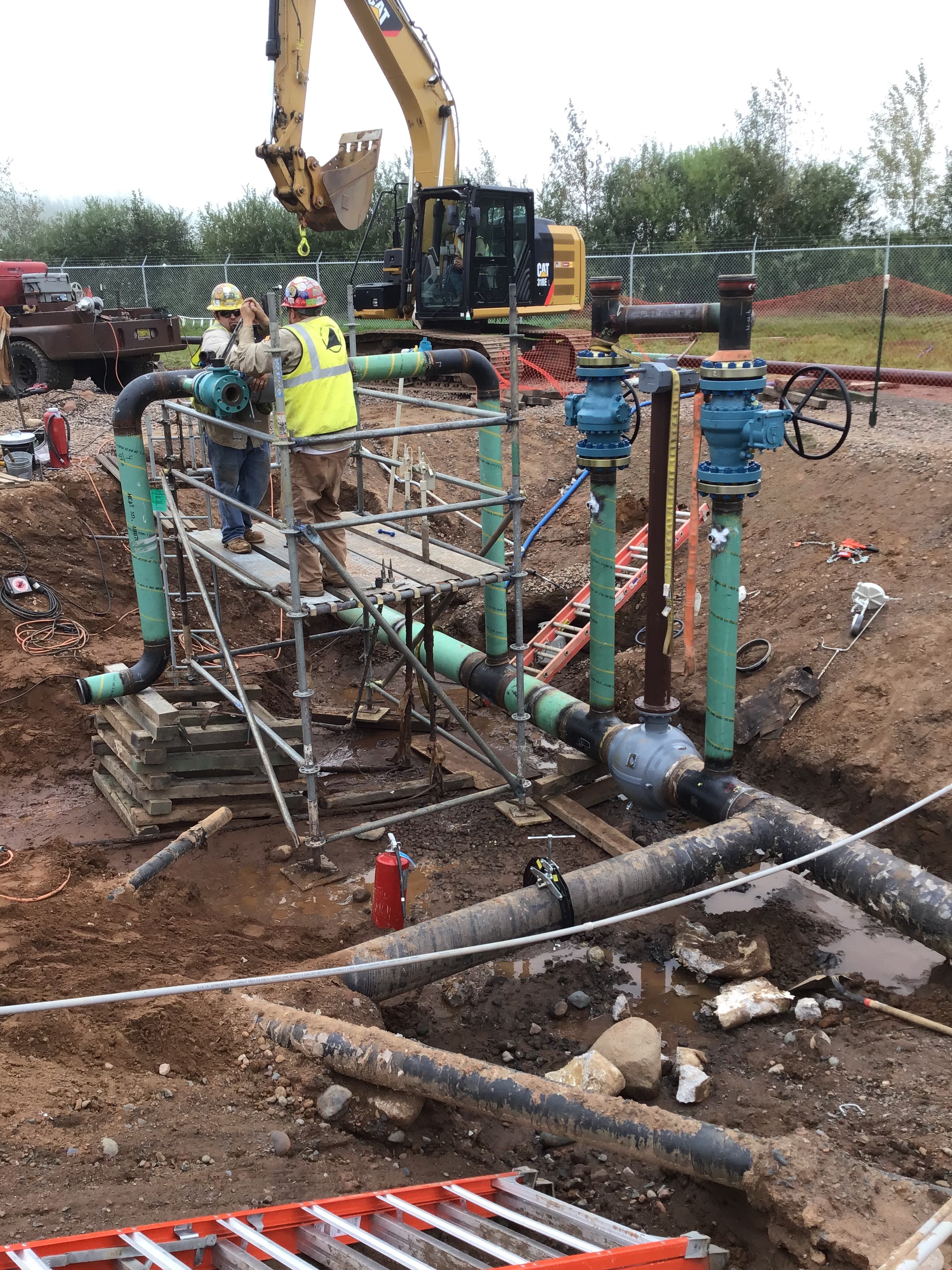
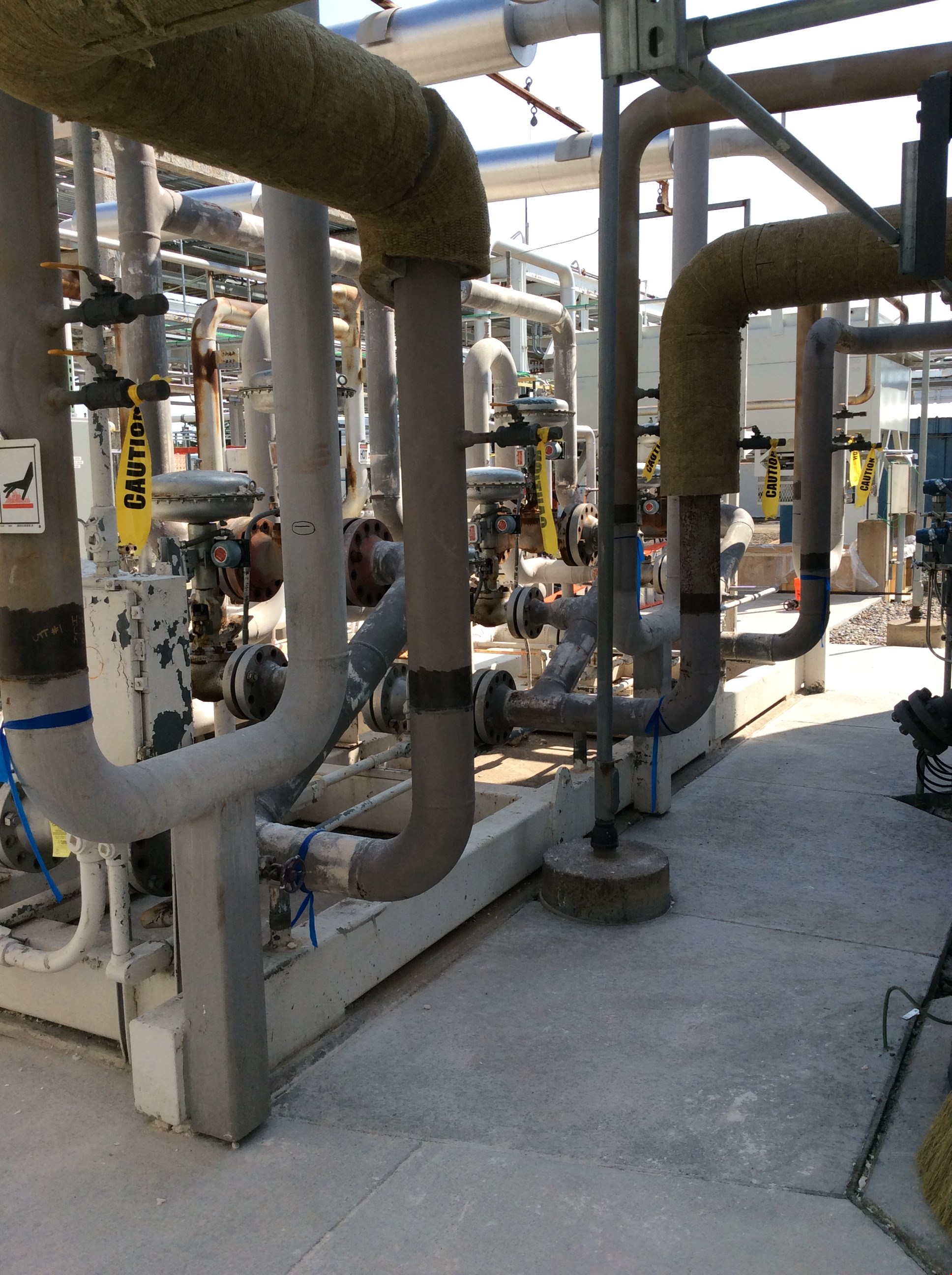
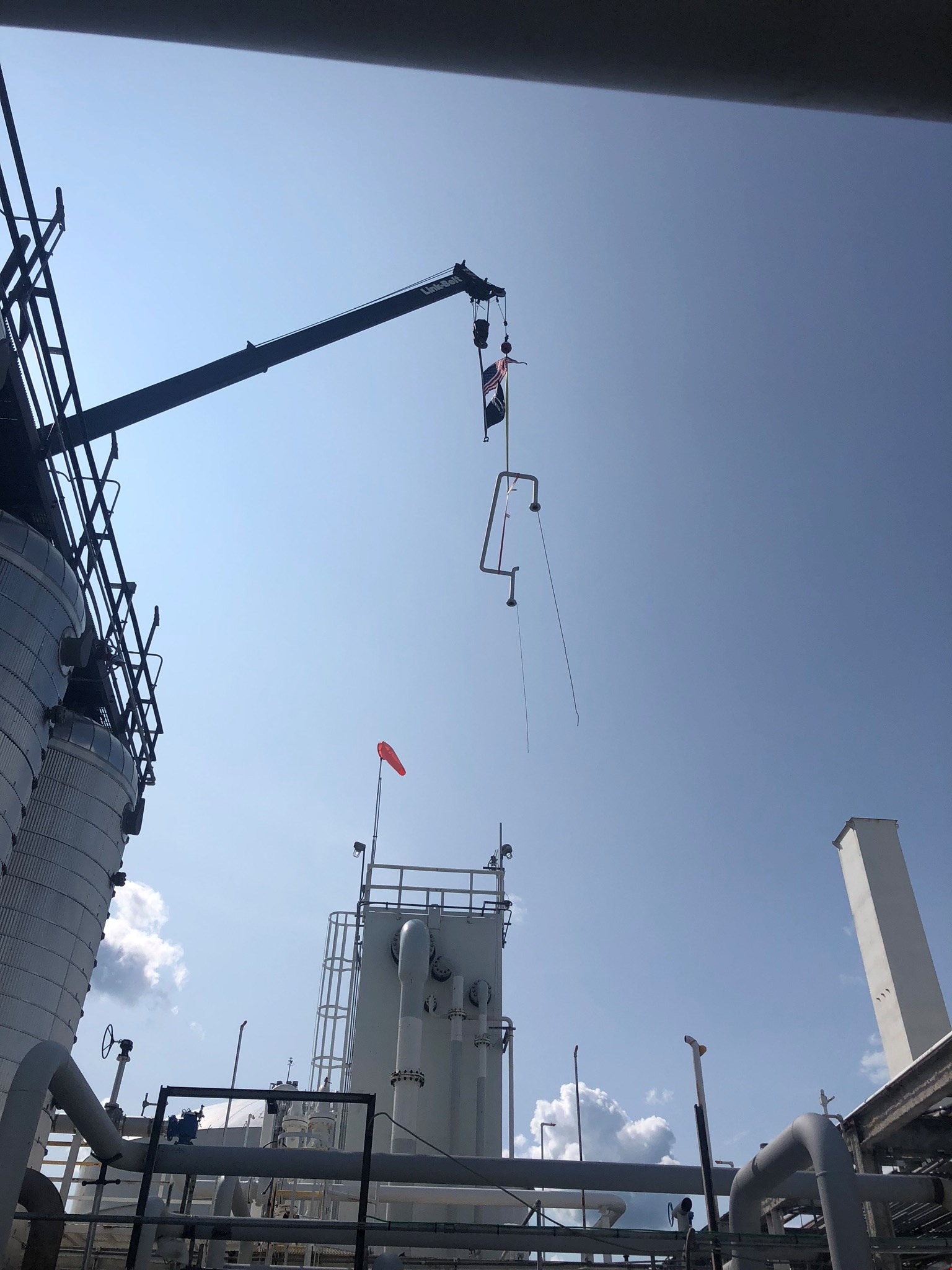

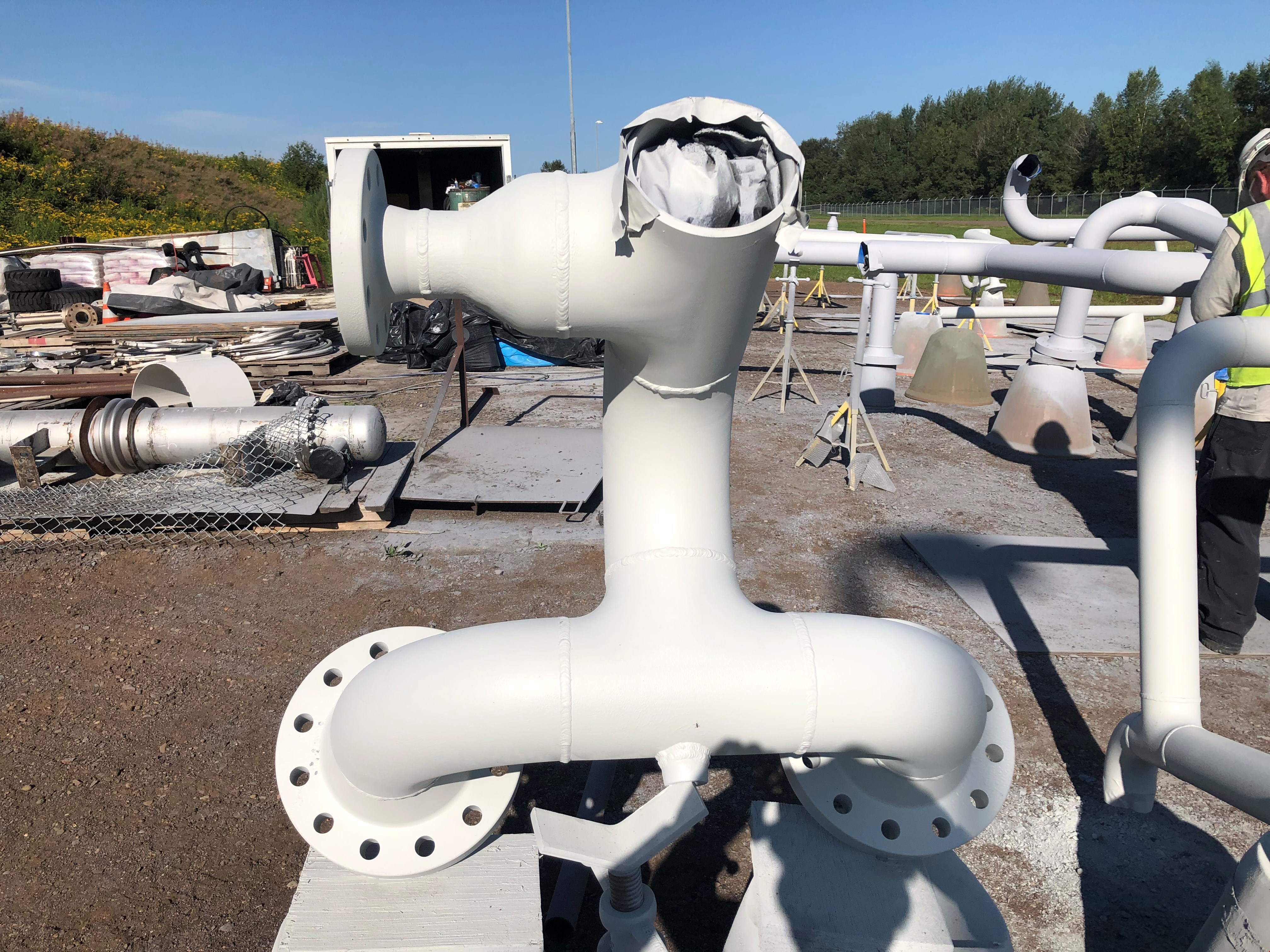